簡介:海底灌注三通,通過性型材料鑄造,能夠在更深層海底作業,減少甚至不用潛水員。機械裝置連接海底管線,并能替代海底焊接作業。該技術已在英國已在工程咨詢公司投入試用,效果不錯。
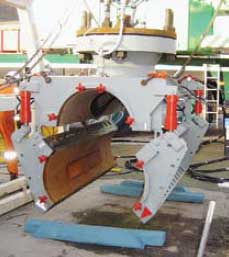
Typical subsea pipeline intervention scenarios are performed with divers. Subsea 7 has been working on the development of a new subsea hot-tap technology, the Subsea Grouted Tee, which will reduce risk, costs and time during intervention operations. The device is a mechanical method of connecting an offtake fitting to an existing pressurized pipeline and is an alternative method to major welding operations.
In 2006, the company realized the potential benefits of this technology and embarked on a Joint Industry Project (JIP) with Advantica, a UK engineering consultancy, to convert the technology for subsea applications. The JIP sponsors (BP, Total and ConocoPhillips) supported the conversion, setting the initial objective of subsea deployment, with the vision of taking it to ultra-deep diverless applications.
The device can tolerate much greater pipeline ovality than some bolt-on mechanical fittings. Since there is a no welding, it offers mechanical integrity and can take loads equal to or in excess of the main pipeline. It incorporates a top half shell with a branch that is either welded or extruded onto the shell during fabrication. The tee branch has a high-pressure, double block-and-bleed Hydrogenated Nitrile Butadiene Rubber (HNBR) seal energized through spreader plates. The lower half of the shell is split into two parts, which are operated hydraulically,
The tee is sized to produce an annular gap between the tee and pipeline. This gap is injected with epoxy grout to create a mechanical bond once it cures, allowing full load transfer between tee and pipeline.
APPLICATION
Conversion of the land-based device to subsea use was performed on a 24-in. stopple branch off a 24-in. pipeline with ANSI Class 900 flange connection for shallow water diver depth operations. A 24-in. x 24-in. stopple prototype was designed and installed in shallow water test tanks using divers and equipment. There were three phases to this work: design/qualification of the tee, design/build of the grout injection system and hyperbaric testing.
Hydraulic pistons compress the main primary saddle seal onto the main pipeline. O-ring sealing strips integrated into horizontal flanges on the doors and the branch half of the fitting provide a gas-tight environment in the annulus between the main pipe and fitting. This enables water to be flushed out with nitrogen when the end seals are activated. These O-rings are temporary and assist with the drying and grout-injection processes.
After the fitting is wrapped around the main pipeline, bolts on the horizontal flanges are preloaded using conventional hydraulic bolt-tensioning tools. This follows the installation of temporary end seals. The annulus is pressure tested to 20 psi. Sea water and annular salt deposits are flushed out with fresh water and dried to below 20% relative humidity using dry nitrogen.
The subsea grout injection unit developed can then be deployed. The skid unit allows various pre-injection testing stages to ensure that the skid settings match ambient subsea conditions. The skid unit has two bladders, one containing resin and the other holding hardener. Each part is pumped independently of and allowed to mix at the built-in static mixer. The pumping process takes about 15 min. After injection, the grout is allowed to set while preparation for hot tap drilling begins. After the grout is cured, a full pressure test is performed on the branch prior to drilling.
FUTURE
Following JIP completion and further development, the technology is now ready for use. The key advantages of this method are:
• No hyperbaric welding
• Elimination of specialist divers
• Shorter lead times
• No pressure reduction requirement
• Cost benefits over other methods
• Emergency situation use
• Future diverless application.
The differences between a welded tee and using the new device indicate that cost savings can be made in pre-qualification exercises and offshore operations. Pre-qualification is not needed, removing pre-heat, NDRT equipment sourcing, habitat modifications, welding/cooling equipment design and diver training. Offshore operations realize savings from installation/removal of habitat and welding equipment, as well as welding/NDT operations.
The device can be used in many scenarios including acute angle branch, multiple branch and K-type configured branches. Possible applications are valve replacement, pipe branch connection, bypass for pipeline repair and blockage removal/introduction of tooling.
Today, diver-assisted branch connections are common, a challenging operation when operating on a pressurized pipeline. At present, the deepest work being performed by divers is at around 250 m. The company’s vision is to provide suitable solutions for pipelines in deep and ultra-deep environments, by deploying this device as a remotely operated technology. Subsea 7 has a worldwide license arrangement with Advantica as the only subsea contractor able to provide this technology.